BM-STAMP
BM-STAMP
汽车冲压仿真软件
BM-Stamp: 汽车冲压模拟的明智之选
在汽车制造早期预测零件质量至关重要,因为当意外缺陷出现且需要在工程周期的后期阶段进行纠正时,依赖实物试模既成本高昂又耗时。
ESI公司的(车身制造 - 冲压,即BM - Stamp)是一种经济实惠的仿真解决方案,它能使汽车零部件制造商优化其冲压工艺,减少对实物原型的依赖,并从项目生命周期的早期阶段就提高制造零件的精度和质量。
BM - Stamp提供了一个极其易用的图形界面,无需工程师具备有限元法(FEM)或其他数值计算方面的专业知识,就能对所有汽车用材料进行精确的冲压验证,从而能够始终如一地实现高度可靠的成形性、精度以及美观效果预测。
ESI 被公认为值得信赖的工程合作伙伴,它能为工程师提供精准的验证,使他们始终如一地达成卓越的模拟效果。因此,能够降低总体成本,并加快生产进度。
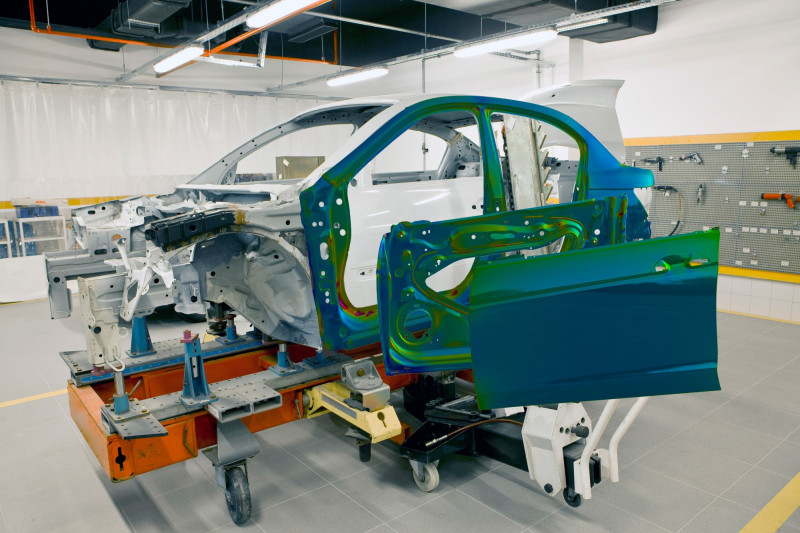

无限次虚拟试验
探索替代冲压工艺路线以及对策的有效性。

无与伦比的预测能力
精准的物理建模,以实现对成型性、回弹和表面美观度的出色预测

直观的界面
用户友好的图形界面,面向冲压工艺的工作流程,完全基于CAD的设置

工艺覆盖范围
专为汽车关键冲压工艺而设计

快速启动
投入生产的准备时间极短;仅需数小时而非数天

经过验证且可扩展
冲压求解器技术拥有超过 25 年的可靠应用记录,具备出色的预测能力和高性能计算能力
我们客户怎么说...
"BM - Stamp 极大地提高了我们的钣金成型模拟精度,尤其是对于像铝这样具有挑战性的材料,” 斯特兰蒂斯(Stellantis)的吉斯兰·库图里耶(Ghislaine Couturier)说道,“对于回弹高达 10 毫米的大型铝制发动机罩内板,它能精准预测 95% 的几何形状,误差在扫描部件的 0.5 毫米以内(见图片)。这种卓越的预测能力,再加上出色的易用性,让我们能够轻松地为超过 25 名用户进行部署,使我们在整个流程中,包括在早期可行性研究阶段,都能显著提高模拟精度。因此,首批部件的几何形状和外观符合率(这是冲压部门的一项关键绩效指标)预计将大幅提升,这将直接降低模具投资成本、减少后期修改率,并缩短项目交付周期。"
Ghislaine Couturier冲压重新经理, Stellantis
BM - Stamp 所带来的关键价值
- 最大限度减少实物试模的成本和时间: 在铣削任何物理工具之前,通过预测和消除成形性问题(如裂纹、皱纹)、补偿回弹和确保所需的外观表面质量来验证冲压工艺。
- 降低你目前用于冲压仿真软件的总体拥有成本:通过价格实惠且灵活的代币许可证,削减你当前的冲压软件预算,或者提升你的计算能力。
- 保证可制造性: 凭借极高的预测可信度,确保设计意图能够实现,同时避免出现制造或外观方面的问题。
- 最小化材料成本:通过精确的坯料轮廓预测。
- 尽量缩短试模与量产之间的时间间隔:提前确保所选冲压生产线生产的零件达到所需质量标准。
- 获得最高的美学品质: 使用专用轮廓来检测可能存在的表面缺陷,并在虚拟光影工作室中进行类似车间现场的分析,以切实评估所识别缺陷的位置、大小和严重程度。
BM-Stamp 主要应用
- 通过对热成型和冷成型金属薄板进行全面的冲压工艺验证,来确认最终零件的质量。
- 通过使用虚拟光影室环境来评估和消除表面缺陷。
- 尽量减少材料的使用和浪费。
- 在冲压过程中,要考虑大型零件和高强度钢部件的弹性模具变形以及压力机变形。
- 预测、控制和补偿回弹(单次或多次操作)。
- 准确确定所需的最小压力,以确保零件可以在选定的压力机上制造。
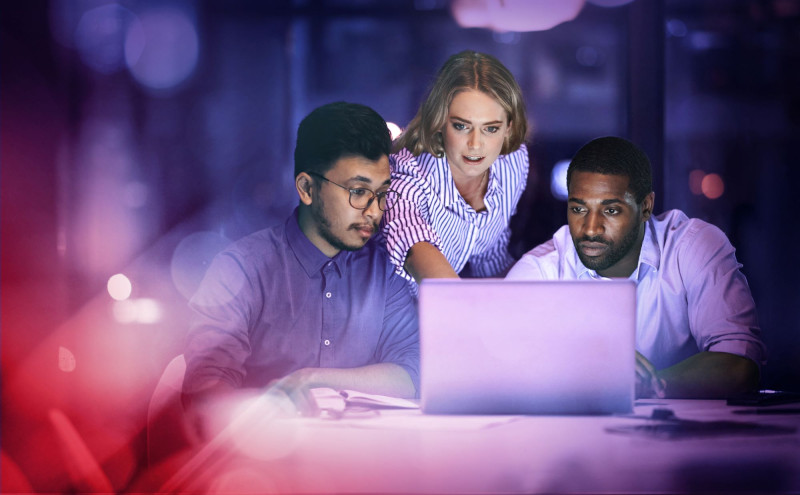
利用 BM-Stamp 仿真的强大功能来处理以下关键的汽车冲压工艺:
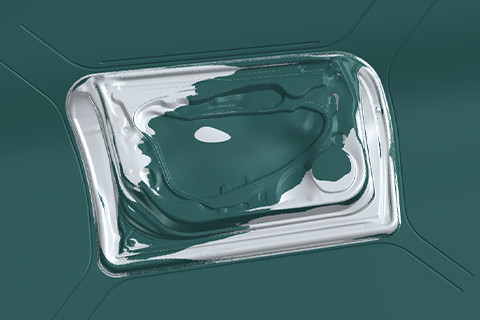
掌握高强度钢和铝合金的加工技术
BM - Stamp 先进的物理求解器能够极为精准地预测可制造性和回弹量,从而满足对强度更高、厚度更薄的高强度钢和铝材的加工需求。
结果? 创新的多操作回弹补偿功能确保每个零件都符合严格的尺寸公差。此外,接触力的精确计算允许轻松评估所需的最小压力,从而便于选择具有足够功率的冲压线来正确生产零件。
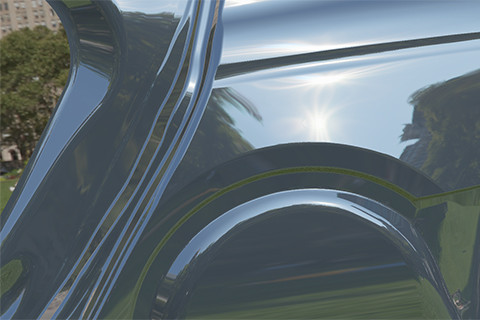
精密提升表面质量
有一系列丰富的专用后处理选项可供使用,用于探究外观缺陷的位置、大小和严重程度。这些选项涵盖了从标准轮廓分析到数字打磨模拟,再到虚拟光影室分析等多个方面,其中还配备了高质量的渲染引擎。
结果? 即使在项目的早期阶段,也要准确预测外观缺陷,以便做出明智的决定并分析拟议对策的有效性,从而大大降低在物理试验中发现缺陷的风险。
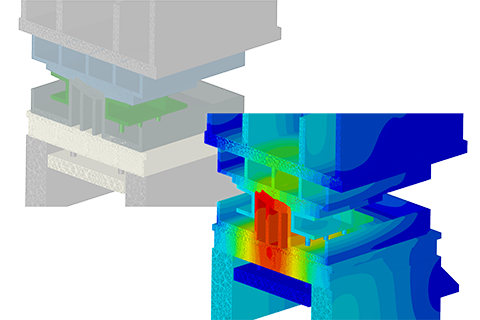
虚拟试模空间
BM - Stamp 将完整的 3D 模具几何形状和详尽的压力机描述集成到标准冲压模拟中,且几乎无需额外的计算时间,能够捕捉到整个冲压过程中模具和压力机的微小弹性变形。
结果? 这种集成提供了最精确的局部接触条件,影响了坯料的材料流动并改变了局部应力场。通过在冲压验证过程结束时进行试验,您可以验证零件是否符合规格,确保始终如一地交付最高质量的产品。
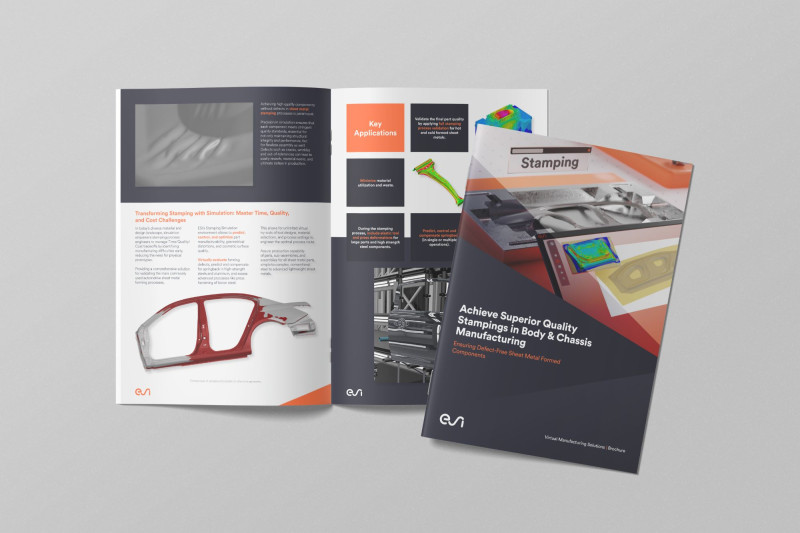